CT Scanner Installation Process Guide
Installing a CT scanner is one of the most important investments a healthcare facility can make.
It opens the door to faster diagnostics, better patient outcomes, and expanded imaging capabilities.
But the CT scanner installation process?
It’s complex.
It requires careful planning, precise site preparation, specialized delivery, and expert calibration.
Any misstep can lead to costly delays or operational issues.
In this blog, there’s everything you need to know about the CT scan installation process. From room prep to first scan, with helpful checklists to keep you on track.
At LBN Medical, we’ve managed CT scan installations in over 15 countries across Europe, Africa, and the Middle East.
Whether you’re setting up a private clinic or upgrading a public hospital, our team ensures your CT scanner is installed smoothly, safely, and in accordance with OEM standards, from day one.
We offer CT scanner installation services for used and refurbished CT systems from GE, Siemens, Toshiba/Canon, and Philips.
Let’s dive into the CT scan installation process.
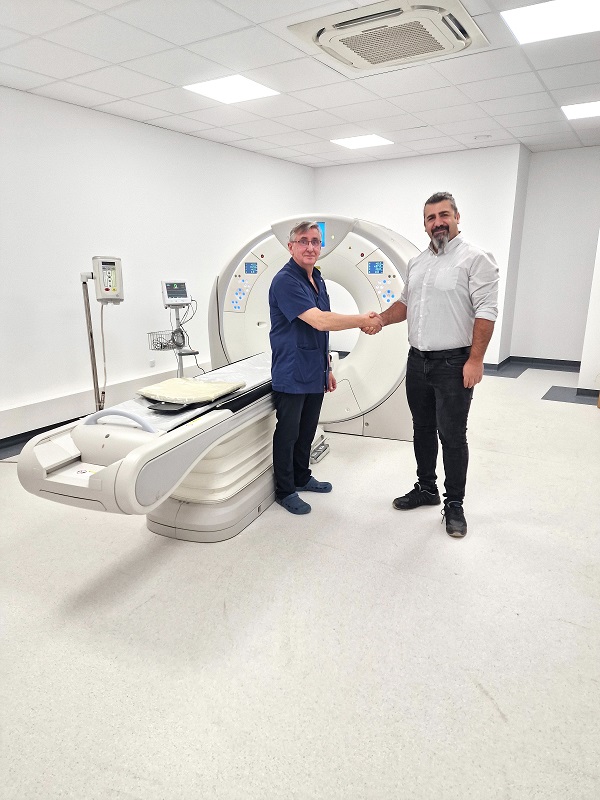
1. Smart Planning Starts the CT Scanner Installation Process
The most successful CT scanner installation begins long before the equipment arrives.
The planning and site assessment phase is critical to ensuring the facility is ready, or identifying what upgrades and adjustments are needed in advance.
This process typically involves a detailed review of the space, power infrastructure, room layout, and technical drawings. Depending on the facility’s location, additional considerations such as access routes, crane requirements, and local health regulations may also come into play.
Key factors to evaluate to meet CT scan installation requirements:
- Room dimensions and ceiling height (2.7–3 meters / 9–10 feet recommended)
- Floor strength and stability
- Location in the building (ground floor or higher)
- Power supply (UPS, power stabilizer, cable sizing)
- HVAC system for proper cooling and airflow
- Noise and dust control
- Permits and compliance with local/OEM regulations
We assist clients during this phase by reviewing drawings, evaluating technical readiness, and offering guidance to ensure full compliance with manufacturer specifications.
2. Preparing the CT Room
Once the planning is complete, the next step is to physically prepare the installation room.
Even the best scanner can fail if the environment isn’t properly controlled.
From technical IT needs to environmental conditions, this step is critical for long-term performance.
CT scan installation requirements include:
- Room layout according to scanner specifications and guidelines (e.g., AERB)
- Fully functional HVAC system for consistent airflow
- Proper ventilation and cooling systems
- IT/network setup (PACS, Ethernet)
- Epoxy-coated or stabilized flooring to support equipment weight
- Lead shielding, lead glass, or other radiation protection (if required)
We work closely with your technical team to confirm that every aspect of the room preparation aligns with system requirements and OEM recommendations.
3. Delivery Logistics
CT systems are large, delicate, and valuable.
That’s why the delivery process needs to be coordinated down to the last detail.
From customs clearance to crate storage and crane lifts, everything should be handled by professionals with experience in handling medical imaging equipment.
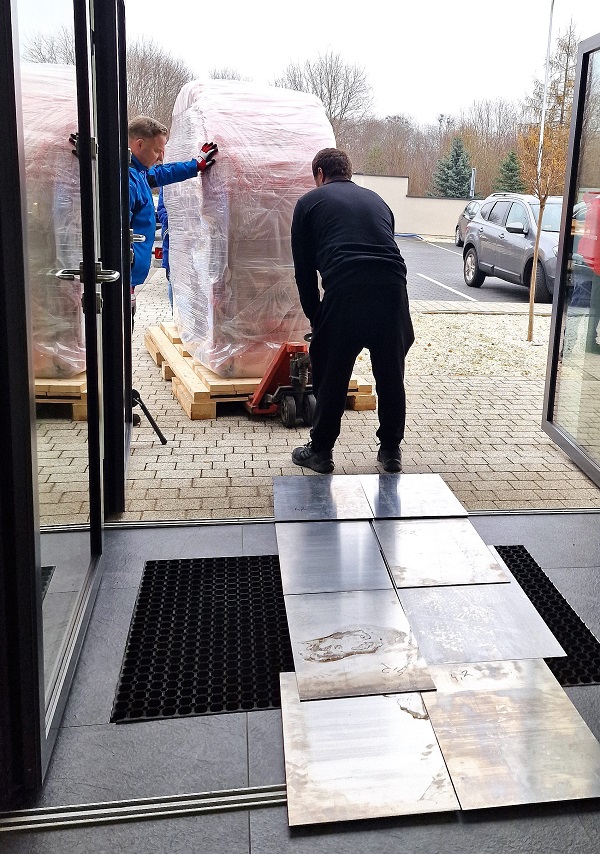
Before your CT scanner arrives:
- Confirm interior access routes and door clearances
- Reserve external loading areas and delivery paths
- Prepare storage for tools/crates shipped in advance
- Plan rigging or crane use for upper-floor installations
- Ensure secure entry for technician and install team
Our logistics team ensures that all components arrive safely and are moved into the correct location efficiently and without disruption.
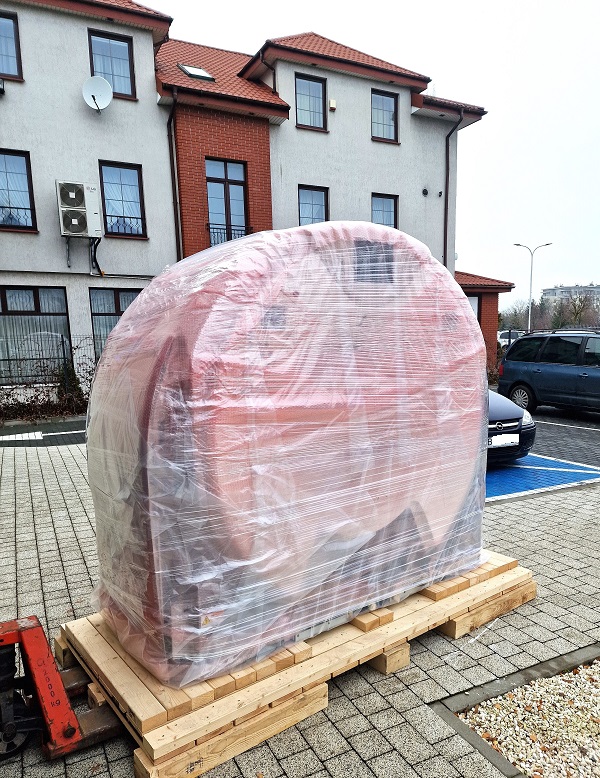
4. Mechanical CT Scan Installation
After delivery, your CT scanner is ready to be installed and assembled.
Certified engineers begin by carefully uncrating the system and inspecting all parts.
They then move and position the gantry and table, connect system cables, and begin mounting the panels and covers.
This phase also includes coordinating with your electrician for final power connections.
Mechanical installation steps:
- Gantry, table, and hardware positioning
- Cable routing and system wiring
- Assembly of covers, mounts, and brackets
- On-site electrician coordination
- Safety checks and final clean-up of the area
We ensure that every mechanical component is installed correctly and securely by trained engineers who follow OEM installation procedures.
5. Calibration & First Scan
Installation alone doesn’t mean your CT system is ready for patients.
The next step is system calibration.
Bringing the machine in line with original manufacturer specifications.
Once the calibration is complete, the engineer performs a first scan to confirm image quality and ensure everything is functioning as expected.
Calibration & testing checklist:
- System calibration to OEM specs
- Verification of performance and accuracy
- First scan performed with test subject or phantom
- Required documentation completed (e.g. FDA Form 2579)
We guarantee that each system is fully functional, compliant, and ready for clinical use before the handover is finalized.
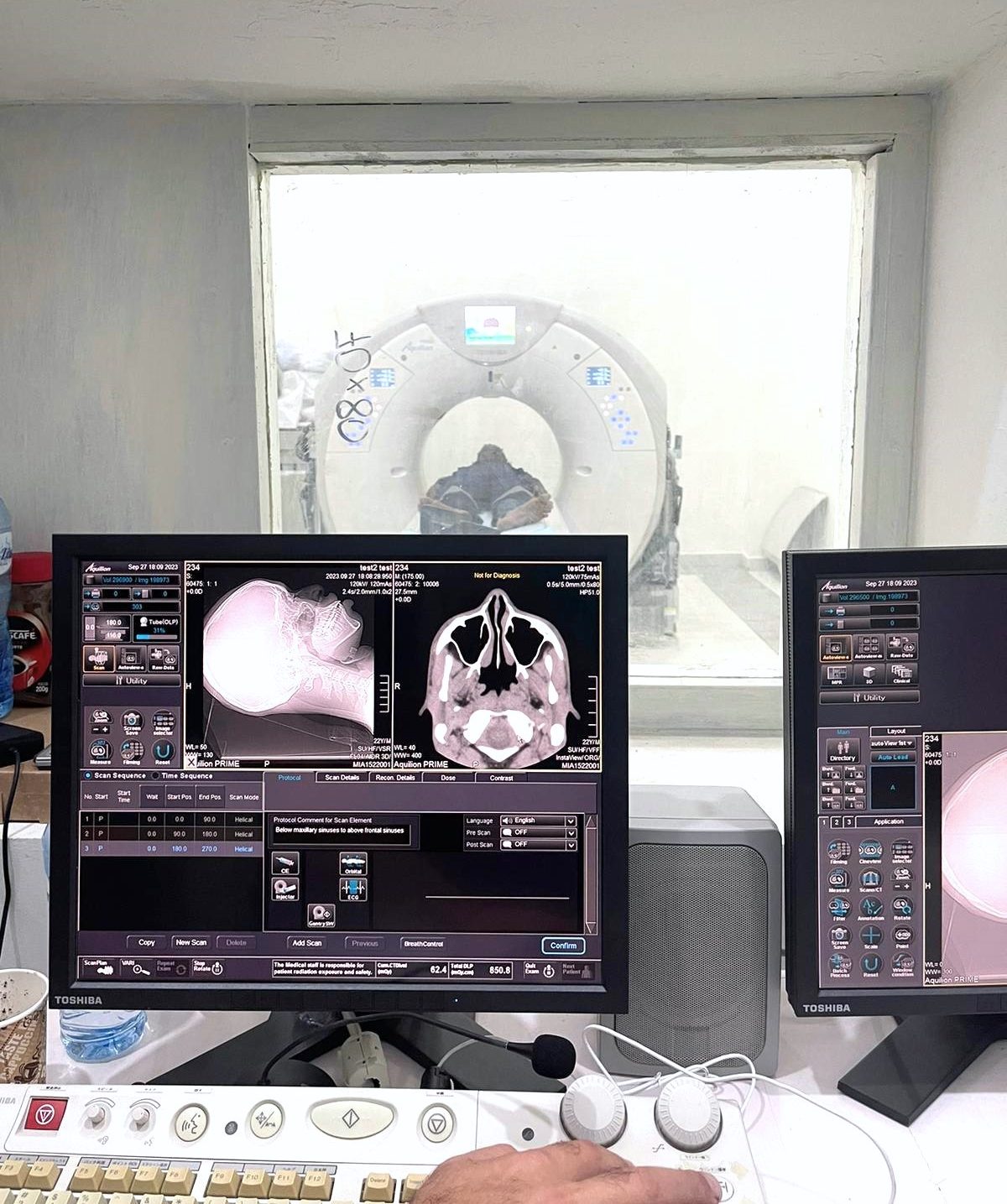
6. System Walkthrough & Handover
Before our technicians leave, they walk your team through a basic System Demonstration of Use.
Showing how to operate the scanner and explaining key components.
This is not full applications training, but it ensures your team is familiar with the basics until official OEM training can be arranged.
Final handover process:
- Basic walkthrough of system operations
- Optional: arrange applications training separately
- Handover form signed by LBN and facility representative
LBN Medical ensures your staff is confident using the system before the final sign-off is completed.
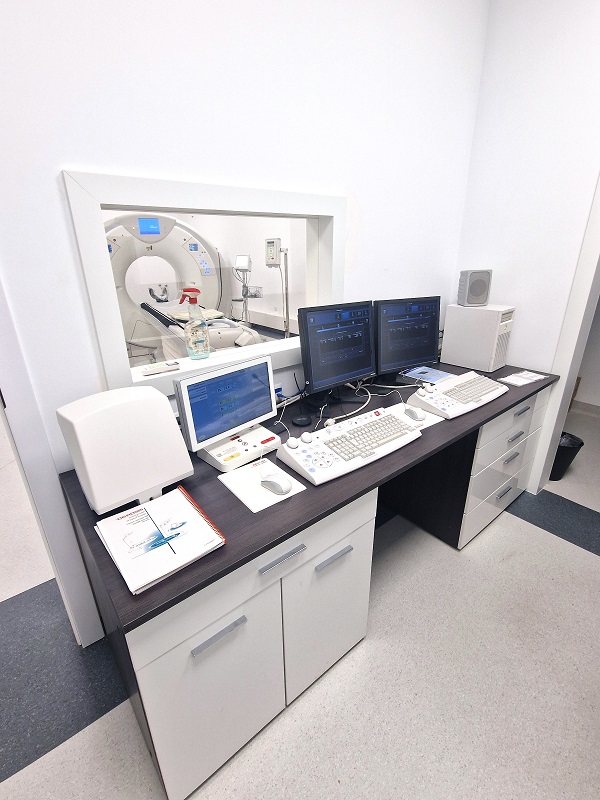
7. Post-Installation Environment Care
Once the scanner is installed, you’ll need to monitor and maintain the room conditions to avoid future issues.
CT systems are sensitive to temperature, humidity, and dust.
Failure to manage those can shorten the system’s lifespan.
Best practices post-installation:
- Ensure dust-free, clean environment
- Keep temperature between 18–24°C (64–75°F)
- Maintain humidity between 30–70%
- Monitor HVAC performance daily
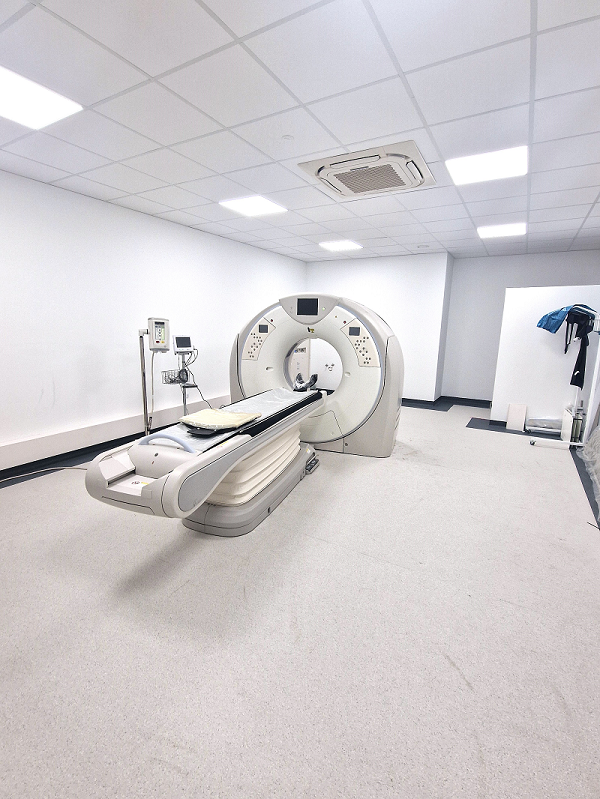
Additional Considerations
If you’re wondering about CT scanner installation cost, pricing varies based on location, scanner model, site readiness, and whether installation is included in your purchase.
At LBN Medical, we provide professional installation services for CT scanners from:
- GE
- Siemens
- Toshiba/Canon
- Philips
If you’re interested in our Gold Package, it is available for Canon/Toshiba CT scanners and the Siemens Emotion 16. Learn more about it below.
For technical teams looking for guidance, we recommend consulting the CT scan machine installation manual that comes with your system.
This OEM-provided documentation includes positioning, power specs, and maintenance instructions.
Our engineers follow these guidelines strictly during installation to ensure compliance and safety.
LBN Gold Package – CT Scanner
Our Gold Package is designed to raise the bar for CT scanner installation services.
It includes all the essential components needed to ensure your CT system is fully operational and seamlessly integrated into your facility:
- 12 months of remote support
- Crating and shipping
- Site visit
- Installation
- One year parts warranty
- Two days of operational training*
- Preventive maintenance
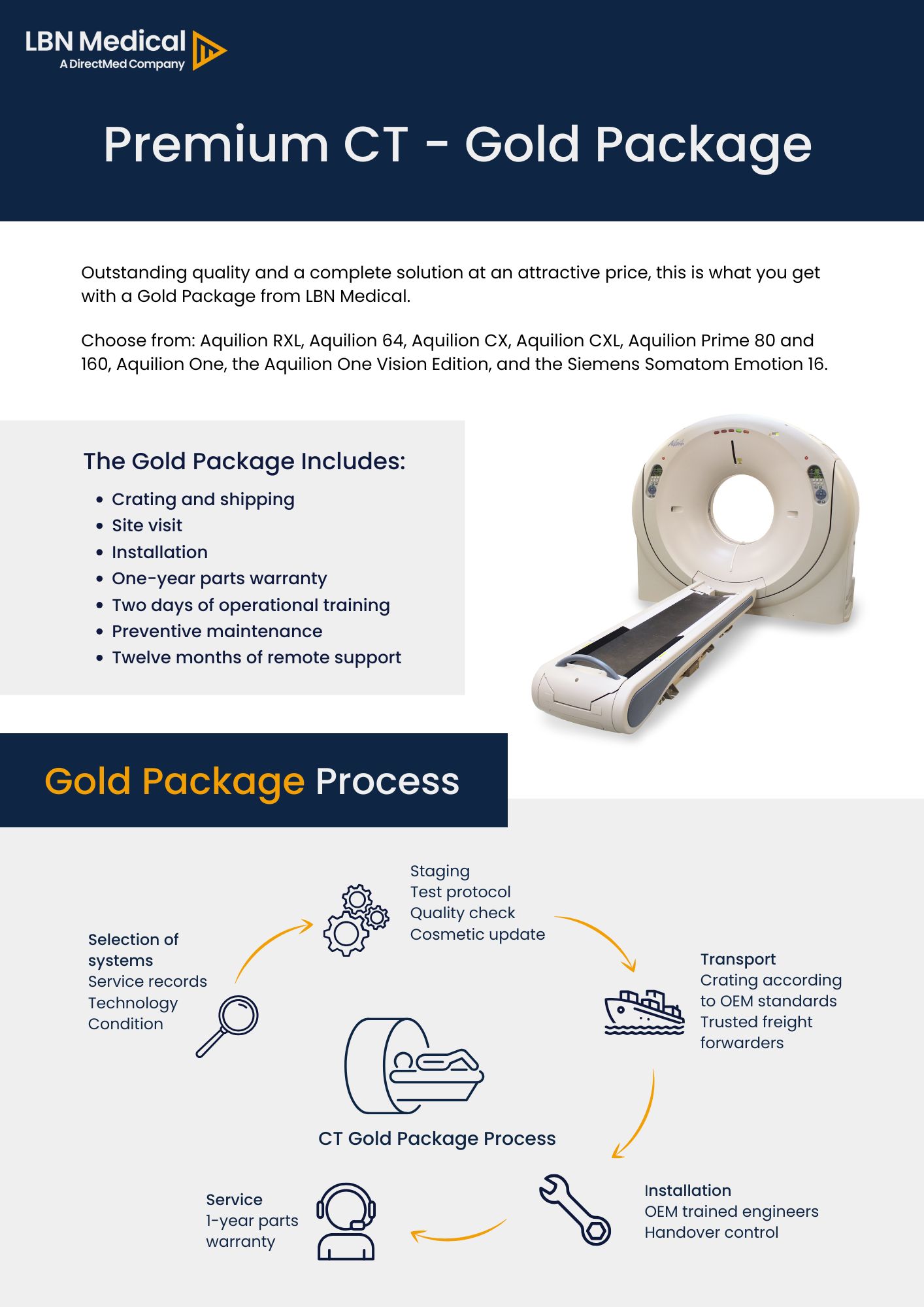
Our CT Gold Package ensures installations are carried out in line with OEM standards. This is made possible by our use of manufacturer-specific procedures and genuine parts throughout the process.
It offers an excellent opportunity for healthcare providers to receive a premium-quality system at a significantly lower cost. A compelling alternative to purchasing a brand-new CT scanner. We typically recondition systems ranging from 16 to 640 slices, including advanced models like the Toshiba Aquilion One.
You can choose from a range of systems, such as:
- Toshiba/Canon: Aquilion RXL, Aquilion 64, Aquilion CX, Aquilion CXL, Aquilion Prime (80 and 160), Aquilion One, and the Aquilion One Vision Edition
- Siemens: Somatom Emotion 16
Designed for facilities that want simplicity and certainty, the Gold Package covers everything from shipping and site planning to full installation and calibration.
All handled through a single point of contact.
Why Choose LBN Medical for Your CT Installation?
At LBN Medical, we understand that you’re not just buying a machine, you’re investing in a medical asset that your team and patients will rely on every day. That’s why we don’t just sell systems, we deliver end-to-end solutions.
With LBN Medical, you get:
- Full-service support: from site evaluation to final handover
- Global expertise with installations in 15+ countries
- Certified engineers and regulatory documentation
- Reliable, high-quality refurbished systems at competitive prices
LBN Medical, A DirectMed company is committed to delivering installations that are smooth, safe, and successful, no matter where you are. Get to know us:
Frequently Asked Questions (FAQ)
How do you install a CT scanner?
CT scanner installation involves several key steps: site evaluation, room preparation, delivery coordination, physical installation, power connection, calibration, and system demonstration. Wen you hire LBN Medical, we manage the full process from start to finish to ensure compliance and optimal performance.
What are the ceiling requirements for a CT scan room?
Most CT scan rooms require a ceiling height of 2.7–3 meters (9–10 feet) to accommodate the gantry and ensure adequate airflow and service access. LBN Medical will confirm exact requirements during the planning phase.
What is required for a CT scan room?
The room must be structurally sound, have proper HVAC and electrical systems, stabilized flooring, and adequate network connections. In some regions, radiation shielding may also be required.
How long does it take to install a CT scanner?
Installation time depends on site readiness and system complexity, but the full process, from delivery to first scan, typically takes between 3 to 5 days once installation begins.
How much does CT scanner installation cost?
CT scan installation including the system can cost between €100,000 and €300,000 for a used CT scanner, and between €300,000 and €900,000 for a new one. These ranges typically include delivery, setup, installation, and initial testing.
Final pricing depends on several factors such as CT scanner model, brand, site readiness, and geographic location. Whether installation is bundled with your purchase also plays a role. To get an accurate estimate, it’s best to request a tailored quote based on your facility’s specific needs.
Final Thoughts: CT Scanner Installation Made Simple
CT scanner installation doesn’t have to be overwhelming.
With proper planning and the right team by your side, it can be efficient, predictable, and rewarding.
Let LBN Medical be your trusted partner, from the first drawing to the first scan.
Contact us today for a quote or site readiness consultation.
Request a CT Scan Installation
Whether you’re looking for just a CT scanner or a complete CT scanner installation, we’re here to support you every step of the way.